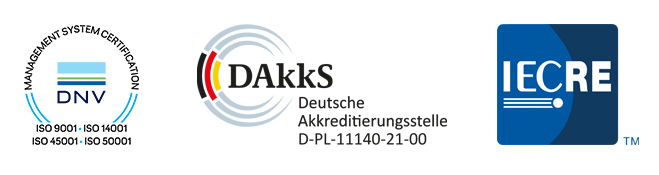
Fraunhofer IWES aims to meet the requirements of its customers at the highest scientific level. Thanks to its quality, occupational health and safety, and environmental management standards, the institute is both process-oriented and cost-efficient. Furthermore, it is firmly aligned to the needs of both its customers and employees.
We are certified to:
* Exception: Technical reliability and Numerical yield and site assessment are certified in accordance with ISO 9001 and ISO 50001.
Our accredited laboratory field measurements is accredited by Deutsche Akkreditierungsstelle (German National Accreditation Body – DAkkS) in accordance with ISO/IEC 17025 with a flexible scope of accreditation per Category A. The laboratory division is permitted to use the test methods listed in the annex to the certificate with different revision dates without prior information or approval from DAkkS.
This provides our accredited laboratory areas with objective and internationally recognized proof of their competence.
We can offer accredited tests in the following test areas:
Our accredited laboratory has been approved for the testing of rotor blades as per IEC 61400-23 by the IECRE committee.
The IECRE System (IEC System for Certification to Standards Relating to Equipment for Use in Renewable Energy Applications) offers an internationally valid certification system for products and services in the renewable energy sector. With this, we also satisfy the very highest safety requirements at the same time.