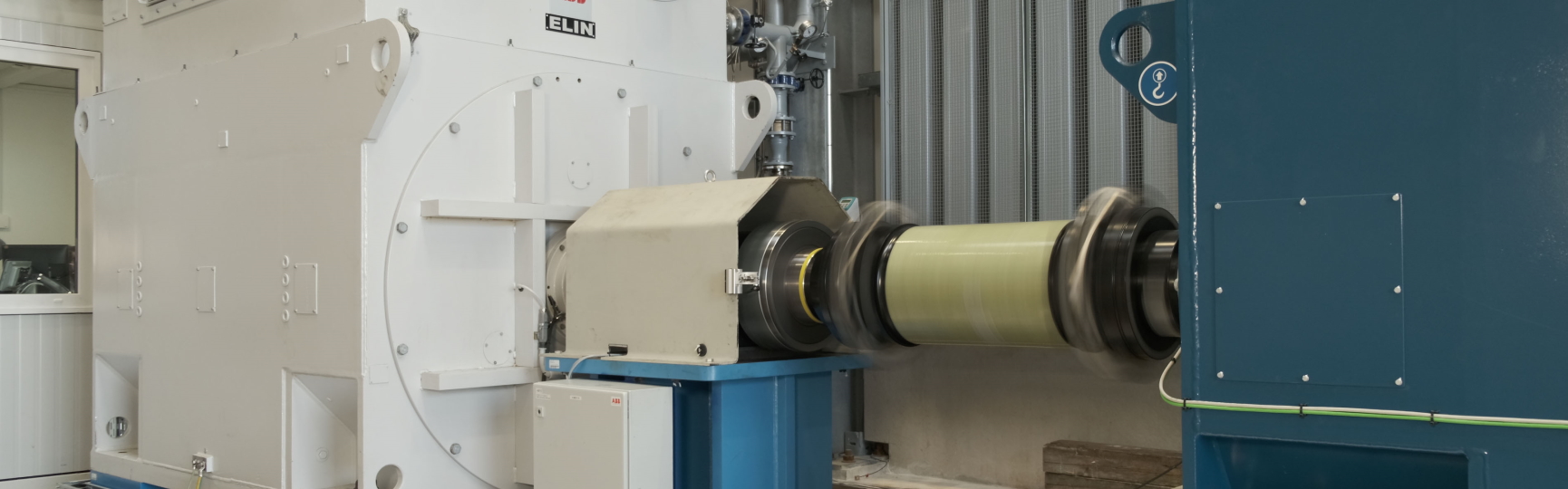
Fraunhofer IWES offers grid compatibility testing for the certification of the electrical properties of new wind turbines (e.g., FRT) and their components. It does so employing a one-of-a-kind virtual grid and medium-voltage grid emulator with a capacity of 44 MVA. The use of this virtual grid enables the simulation of all typical grid faults. This approach makes it possible to conduct static tests, for example to record the active and reactive power output under different grid conditions and to simulate transient grid events.
In addition, IWES also has the capacity to determine the electrical properties of frequency converters. The PQ4Wind test bench is employed to measure the high-frequency power quality.
As offshore wind turbines continue to grow in size, the current facilities for testing grid characteristics are being pushed to their limits. For this reason, IWES has developed a mobile grid emulator with an installed converter capacity of 88 MVA, which can test the electrical properties of wind turbines and their ability to support the power grid in the event of faults in the field (e.g., at prototype installation locations).
The higher share of feed-in from renewable sources in the distribution and transmission grid structures at various voltage levels is seeing the requirements for the grid integration of wind turbines as power generating units (PGUs) increase even further. These are reflected in standards and guidelines that will have to be taken into consideration in the future. System certificates are expressly required for the connection of new and further developments. They ensure grid-compliant operation of the PGUs and guarantee the permanent grid connection.
IWES provides system manufacturers with support in satisfying the increasing requirements by offering efficient test methods for accelerated validation of the electrical properties of PGUs on test benches.
Status quo: field tests with little informative value.
Grid compatibility testing for the certification of the electrical properties of new wind turbines – or for subsequent certification in the case of modifications or further developments of existing turbine types – is currently performed almost exclusively with the aid of simple mobile test equipment in the field. However, field tests are difficult to reproduce – the results depend highly on local grid and weather conditions, meaning they can only be compared for validation to a limited extent.
2015 saw the opening of Germany’s biggest large-scale test bench for complete wind turbine nacelles. The Dynamic Nacelle Testing Laboratory (DyNaLab) offers a realistic test environment for nacelles. The HiL-GridCoP test bench, opened in 2021, allows generator-converter tests in the multimegawatt range performed as meaningful laboratory tests. One-off test services for prototype validation are offered with a drive power of 10 MW. The 44 MVA grid emulators and HiL wind load simulations make it possible to create different real load scenarios under reproducible conditions. For example, it is possible to test the behavior of a wind turbine with multi-dips in the grid during a storm, grid short circuits due to faulty pitch control, or emergency stops.
In addition to certification in the laboratory, the test benches thus offer the possibility of considerably shortening formerly lengthy certification processes and performing measurements for grid codes that exist worldwide, as different operating scenarios can be run on the test benches as often as required. In this way, operational management and control can also be optimized and model validations performed targetedly.
In addition, IWES also has the capacity to determine the electrical properties of frequency converters in a cost-effective manner, with the wind turbine system including the generator being replaced by corresponding simulation models (pHiL approach). This converter test bench is employed for high-frequency measurements as well as for the testing and optimization of grid-forming properties of DUTs/converters.
As offshore wind turbines continue to grow in size, the current facilities for testing grid characteristics are being pushed to their limits. For this reason, IWES has developed a mobile grid emulator. This can be employed to test the electrical properties of wind turbines using conventional measurement methods as well as to test and verify all currently discussed approaches for model validation and verification of control behavior in the field (e.g., at prototype installation sites). For this purpose, the test system can be connected between the wind turbine to be tested and the local grid, thus enabling high-quality and reproducible measurements of the grid properties.
Test rig HiL-GridCoP - Electrical system testing in the laboratory
Power converters are designed to withstand their typical operating conditions. In the field, however, they are exposed to a wide variety of influences which can induce failure. In wind energy, for instance, the failure rate of power converters is as high as 0.5 damage-related failures per wind turbine and year.
As humidity has been found to be a major driver of failures, we set up a laboratory to validate clients’ products from power modules to entire converter systems under real site scenarios and harsh conditions. Fraunhofer IWES joined forces with the Institute for Electrical Drives, Power Electronics and Components (IALB) of the University of Bremen to run the HiPE-LAB – a unique facility for testing converters up to 10 MVA under a superposition of application-specific climatic and electrical loads.