Ten years BladeMaker: Industrialized rotor blade manufacturing
09/14/2023, Berlin – Fraunhofer Institute for Wind Energy Systems IWES began researching the topic of automated rotor blade manufacturing ten years ago with the start of the »BladeMaker« project. The follow-up project »BladeFactory« is set to be completed this October. This marks an important occasion for the project team to look back at the results and identify future trends in rotor blade manufacturing together with project partners and guests from the wind energy industry and research sector. The BladeMaker project was funded by the German Federal Ministry for Economic Affairs and Climate Action (BMWK) to the tune of around €8 million and the BladeFactory project with around €9 million. The final conference with around 40 guests was held on Tuesday at ENIQ on the EUREF-Campus in Berlin.
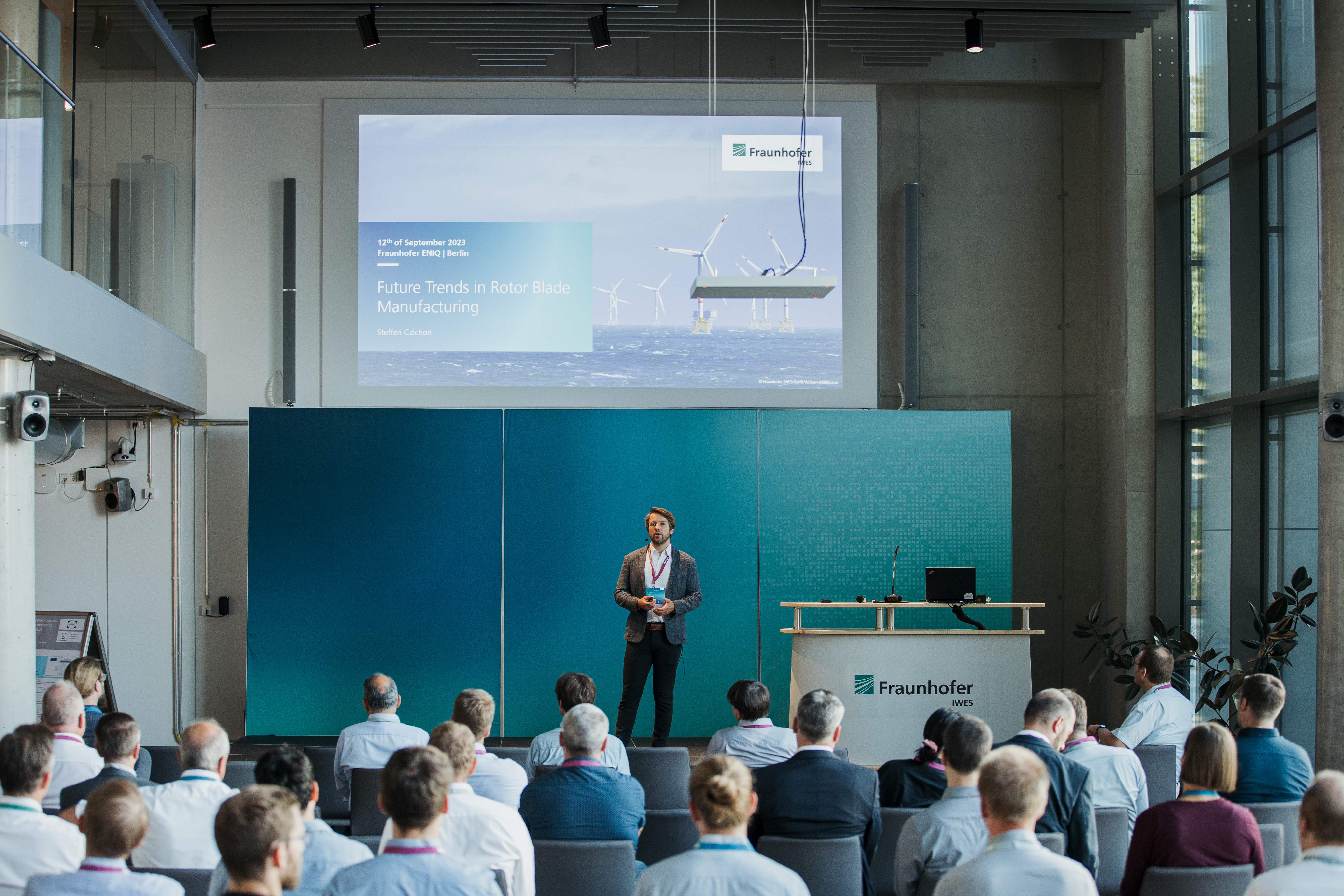
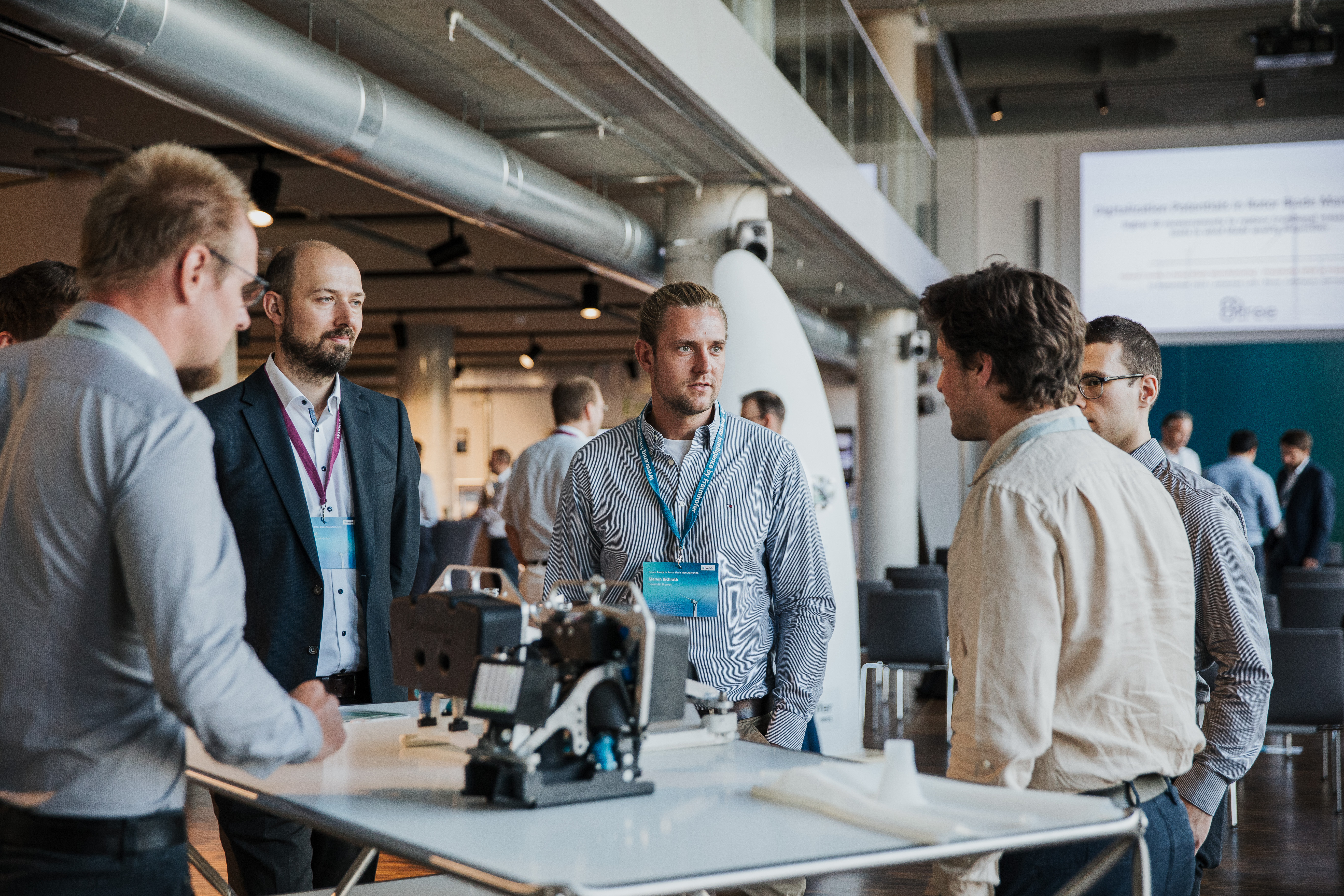
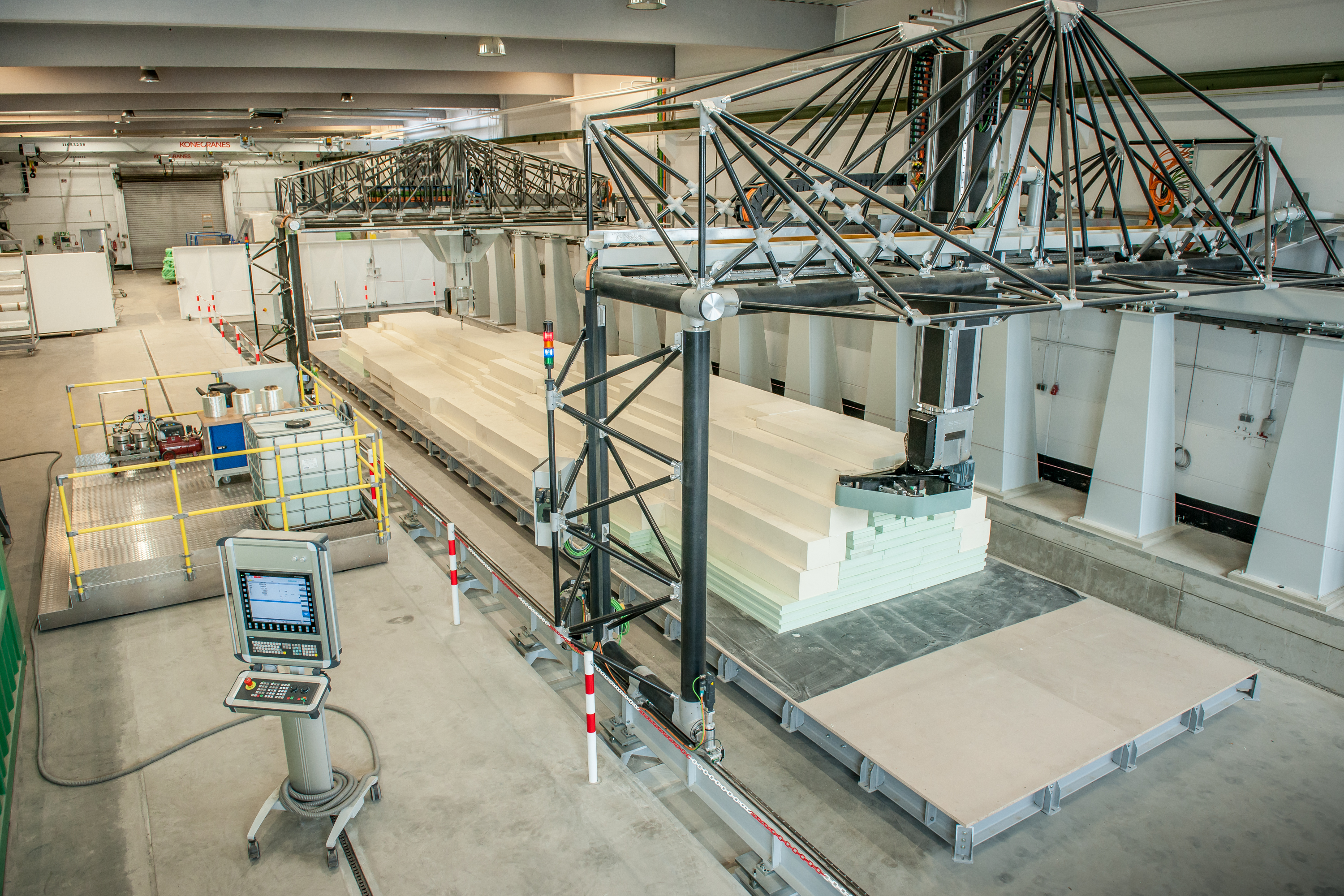
Rotor blades account for around 20% of the total costs of a wind turbine. New materials and optimized processes should be utilized to optimize the manufacturing process even further and boost the quality – there is still a considerable amount of untapped optimization potential in the production chain. The goal is to produce rotor blades for wind turbines more sustainably, faster, and more reliably – and that as inexpensively as possible.
Setting up of the test environment at the BladeMaker DemoCenter
As part of the BladeMaker research project, Fraunhofer IWES has built and commissioned the BladeMaker DemoCenter in Bremerhaven over the last ten years, creating a realistic test environment in which holistic processes can be developed to further automate and industrialize rotor blade manufacturing. When doing so, the scientists investigate the rotor blade design, materials, and manufacturing processes to test the potential for implementing automation. Until now, many rotor blade manufacturing steps are performed one after the other and still manually in the main mold tool of the rotor blade blank. Among other things, the project team has succeeded in constructing a mold tool without first creating a 1:1 master model of the blade. Omitting this intermediate step allows manufacturers to shorten the production time by around two months. In addition, the use of an integrated software solution makes it possible to simulate 3D models of the individual components and thus prepare the manufacturing process with precision. The project also saw the development of a complex gantry robot on which different process heads can be installed and controlled in different ways: working steps such as milling, gluing, and grinding as well as the impregnation of the fiberglass fabrics can thus be tested in an automated manner. The BladeMaker DemoCenter was officially opened in 2017.
Automated solutions for rotor blade production
The goal of the scientists in the follow-up project BladeFactory was to further develop and parallelize the sub-processes and procedures. The individual process steps are to be integrated one by one into a coherent overall process: For example, the past five years have seen the development of the automated process of preforming, the automatic depositing and draping of fiber fabrics and core materials, and prefabbing, the prefabrication of rotor blade components. These processes also help to shorten production time, as they can be outsourced from the main blade mold tool and thus implemented in parallel.
The processes are accompanied by the use of measurement technology and mechanical testing to ensure reproducible quality. In addition, the researchers are utilizing a laser measurement system that records the 3D geometry of the finished components. The manufacturing process is becoming more efficient.
Heiko Rosemann, Project Manager at Fraunhofer IWES, explained: »Today, we are celebrating the milestones of the past ten years. With our processes, we have been able to contribute considerably to shortening the production times for rotor blades and simultaneously improving the quality of the component. This reduces the risk of expensive reworking and material surcharges for the customer. We can produce a mold tool directly and even control and shorten the adhesive curing process with an integrated cooling function. The use of our Variable Glue Applicator means it is no longer necessary to change tools when gluing the shells and allows adhesive savings of up to 20%. We are proud of what we have achieved and look forward to developing solutions for the challenges ahead together with the industry.«
»The speeding up of production processes and saving of material are some of the key tasks in rotor blade development. The test environment at the BladeMaker DemoCenter allows investigation of all aspects of automated production, which helps the industry to further optimize these processes. Fraunhofer IWES is making an important contribution to research and development with its work,« said Dr. Alexander Krimmer, Senior Engineer Composite Materials and Structures, TPI Composites Germany.
»The expertise of the IWES scientists plays a major role in enabling manufacturers to test new production processes and implement them on a large scale. With IWES’ help, we have been able to qualify our adhesive application and investigate what effects temperature and humidity have in blade production. The results allow us to make our adhesive process even more efficient,« added Kai Ehrich, Group Lead Materials, Nordex Energy.
The test environment at the BladeMaker DemoCenter is being continuously expanded and also enables scientists to work across different groups. For example, special components made of fiber composites are also manufactured here for the rotor blade tests next door and sensory measurement technology is being developed.
___
Contact person at the Fraunhofer Institute for Wind Energy Systems IWES
Project Manager: Heiko Rosemann, Research Associate, Department Rotor Blades
Tel.: +49 (0)471 14290-341
E-mail: heiko.rosemann@iwes.fraunhofer.de
www.iwes.fraunhofer.de
Contact person at TPI Composites Germany GmbH
Dr. Alexander Krimmer, Senior Engineer Composite Materials and Structures
Tel.: +49 (0)30 311 92-212
E-mail: a.krimmer@tpicomposites.com
Contact person at Nordex Energy GmbH
Kai Ehrich, Group Lead Materials
Tel.: +49 (0)381 66633688
E-mail: KEhrich@nordex-online.com
Fraunhofer IWES
Fraunhofer IWES secures investments in technological developments through validation, shortens innovation cycles, accelerates certification procedures, and increases planning accuracy by means of innovative measurement methods in the wind energy and hydrogen technology sectors. There are currently over 300 scientists and employees as well as more than 100 students employed at nine locations: Bochum, Bremen, Bremerhaven, Görlitz, Hamburg, Hannover, Leer, Leuna, and Oldenburg.
TPI Composites Germany GmbH
TPI Composites, Inc. is a global company focused on innovative and sustainable solutions to decarbonize and electrify the world. TPI delivers high-quality, cost-effective composite solutions through long-term relationships with leading OEMs in the wind and automotive markets. TPI is headquartered in Scottsdale, Arizona and operates factories in the U.S., Mexico, Türkiye and India. TPI operates additional engineering development centers in Denmark and Germany and global service training centers in the U.S. and Spain.
Nordex Group
The development, manufacture, project management and servicing of wind turbines in the onshore segment has been the core competence and passion of the Nordex Group and its more than 9,600 employees worldwide for over 35 years. As one of the world's largest wind turbine manufacturers, the Nordex Group offers high-yield, cost-efficient wind turbines that enable long-term and economical power generation from wind energy in all geographical and climatic conditions.
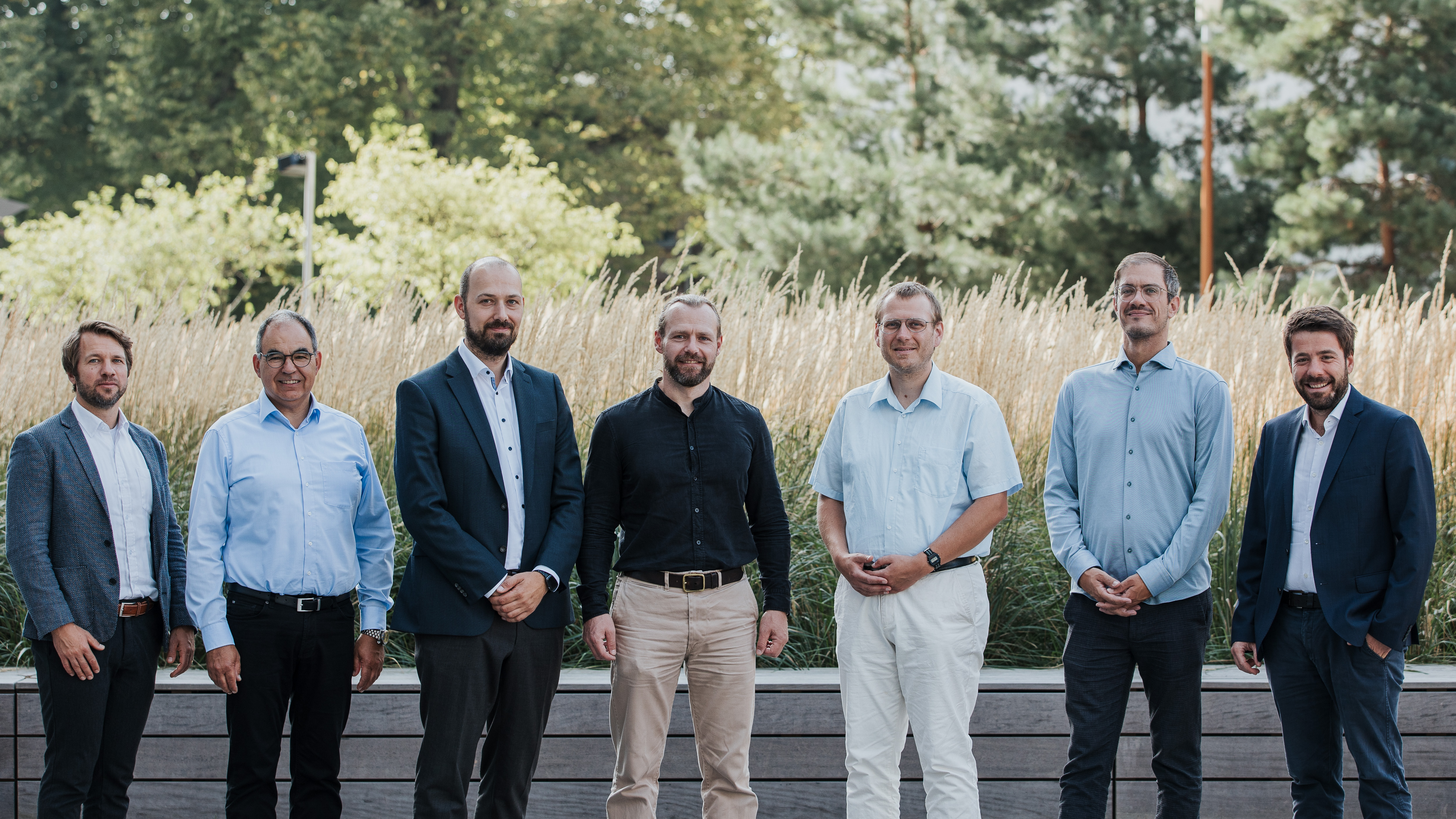

Last modified: